The light industrial sector is on the cusp of a groundbreaking transformation with the advent of Industry 4.0 technologies. Industry 4.0, characterized by the convergence of digital and physical systems, has been revolutionizing the way businesses operate, ushering in a new era of efficiency, productivity, and safety. In this article, we will delve into the impact of Industry 4.0 on the light industrial sector and explore how it reshapes the roles of workers.
Understanding Industry 4.0 and Its Technological Advancements
Industry 4.0 represents the fusion of cutting-edge technologies, such as the Internet of Things (IoT), Artificial Intelligence (AI), Big Data analytics, and robotics, to create intelligent and interconnected systems. Unlike previous industrial revolutions, Industry 4.0 is defined by its ability to enable real-time data exchange between machines, facilitating autonomous decision-making and seamless communication across the entire manufacturing process. This digital transformation promises to unlock unparalleled potential for the light industrial sector.
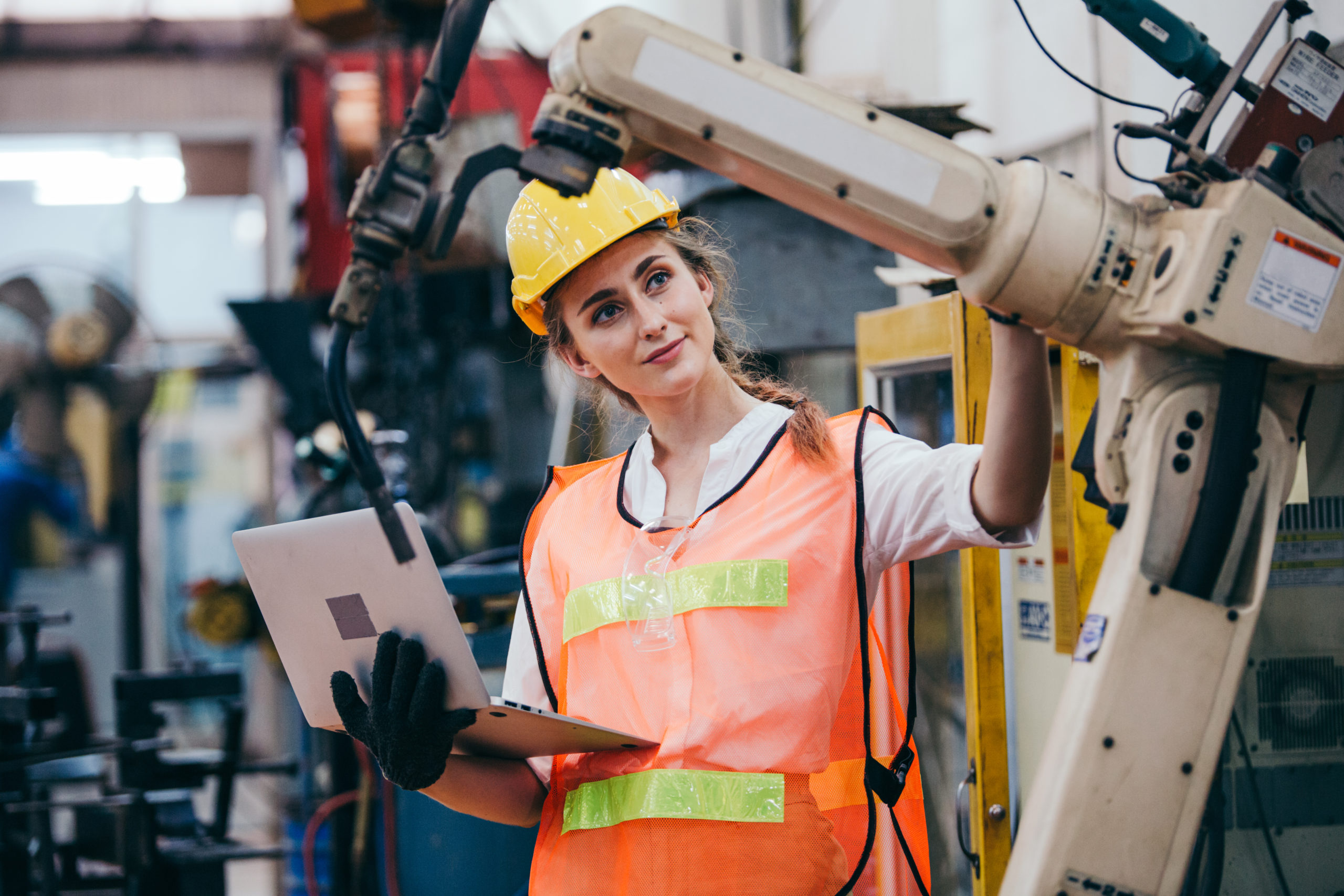
The Impact of Industry 4.0 on the Light Industrial Sector
One of the most visible impacts of Industry 4.0 in the light industrial sector is the increased use of automation. Robots and machines are now taking on many of the repetitive and dangerous tasks that were once performed by human workers. This has led to a number of benefits, including higher production output, reduced labor costs, and improved safety.
Another key impact of Industry 4.0 is improved efficiency and productivity. Data-driven decision-making is now possible thanks to advanced analytics and machine learning algorithms. This allows businesses to optimize their operations, minimize downtime, and improve overall efficiency. Real-time insights also enable businesses to respond more agilely to production demands, enhancing productivity to unprecedented levels.
The integration of AI and IoT devices is also enhancing safety measures in light industrial workplaces. Smart sensors monitor equipment performance, identify potential risks, and preemptively address safety concerns. This has led to a significant reduction in the occurrence of workplace accidents and injuries.
“Beyond workplace technological advancements, wearable devices are now being used by the labor force to accomplish previously time consuming or manual processes,” Stephen Grimaud, Partners Personnel VP of Risk Management said. “Some wearable devices can be used to help with accident avoidance, detection and notification. Other wearable devices can tell you whether ergonomic improvements can be achieved during physical activities as well as provide vital sign monitoring and reporting.”
Finally, Industry 4.0 is helping to reduce costs and optimize resource usage. Data-driven insights can help identify inefficiencies and optimize resource usage, leading to significant cost reductions. These optimizations can also contribute to sustainable and responsible practices.
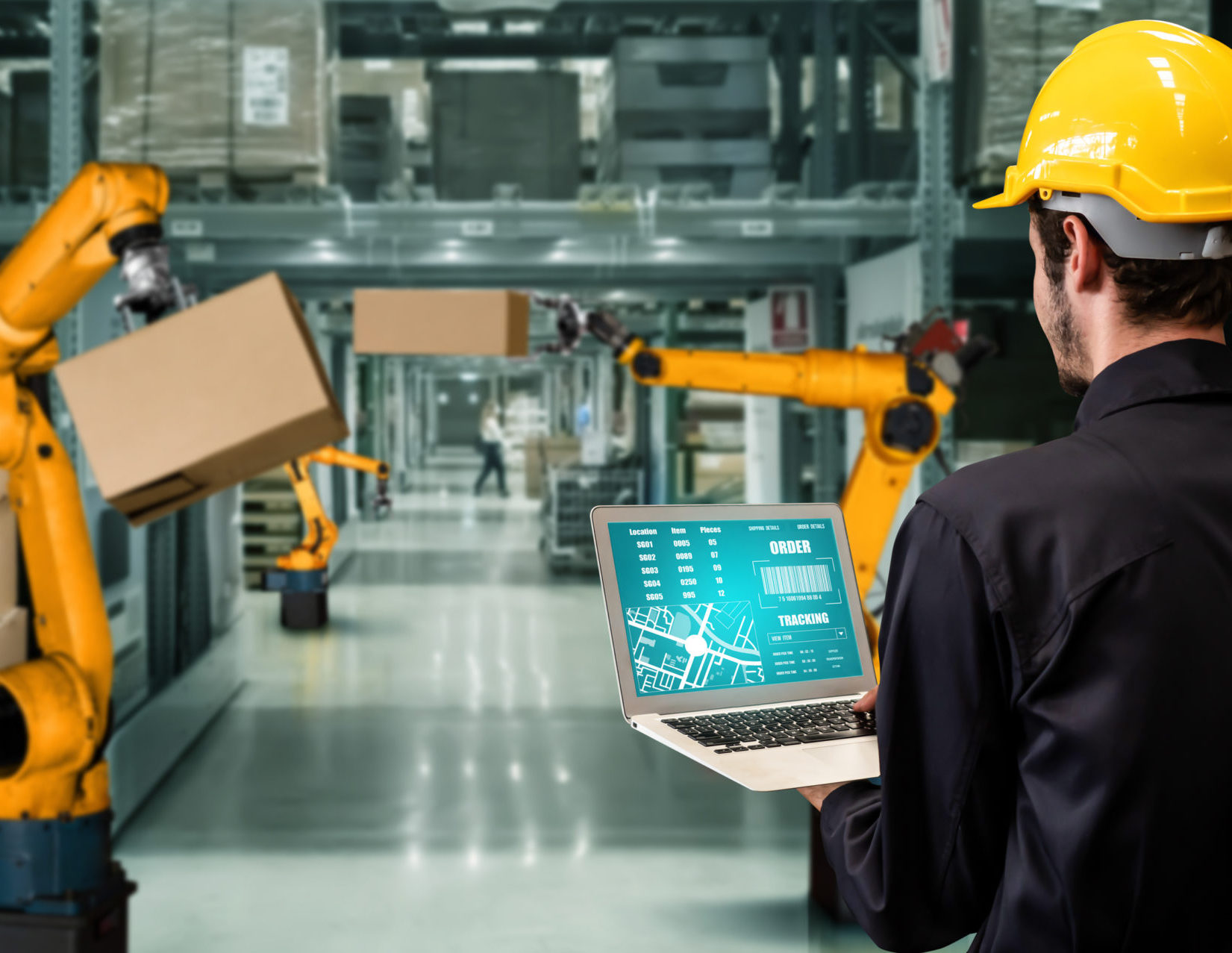
Evolving Roles of Workers in the Light Industrial Sector
Industry 4.0 introduces a shift in the skills required of light industrial workers. Soft skills, such as problem-solving, critical thinking, and adaptability, become increasingly valuable alongside technical proficiency. Additionally, workers are no longer simply operators but collaborators with intelligent machines. The seamless interaction between humans and robots enables a new level of production harmony, where machines assist and augment human capabilities.
Further, as automation assumes routine tasks, employers must invest in reskilling and upskilling their existing workforce. By nurturing new skill sets, companies can foster a more agile and versatile workforce, capable of embracing Industry 4.0 innovations. And with that comes a rise of new job roles, such as data analysts, automation engineers, and IoT specialists. These roles bridge the gap between technology and operations, forming a dynamic workforce.
The Challenges of Industry 4.0
In preparing for the future of work in the light industrial sector, there are several challenges that companies must address and overcome. One significant challenge is workforce disruption, as the integration of Industry 4.0 technologies may disrupt traditional job roles. This requires thoughtful management of workforce transitions, ensuring that employees are supported and guided through changes in their responsibilities and tasks.
Another critical challenge is data security and privacy. With data becoming a critical asset in the Industry 4.0 era, companies must prioritize safeguarding sensitive information to mitigate potential risks. Implementing robust data security measures and adhering to privacy regulations are essential to maintain the trust of customers and stakeholders.
The successful adoption of Industry 4.0 technologies also hinges on overcoming resistance to change. Technological adoption requires thorough training and guidance for employees to embrace new systems and processes effectively. Providing the necessary resources and support during this transitional phase is vital for a smooth and successful implementation.
How Can Employers Gain a Competitive Edge
To truly generate an industrial workforce for the future, several key initiatives must be embraced. Leadership plays a pivotal role in driving technological transformation and encouraging a culture of innovation. Strong and visionary leadership is crucial in guiding the organization through the dynamic changes brought by Industry 4.0.
Collaborating with educational institutions is another vital aspect of workforce preparation. Establishing partnerships with these institutions helps create targeted upskilling programs tailored to the demands of Industry 4.0. By aligning educational initiatives with the needs of the evolving workforce, companies can cultivate a skilled workforce that is well-prepared for the future.
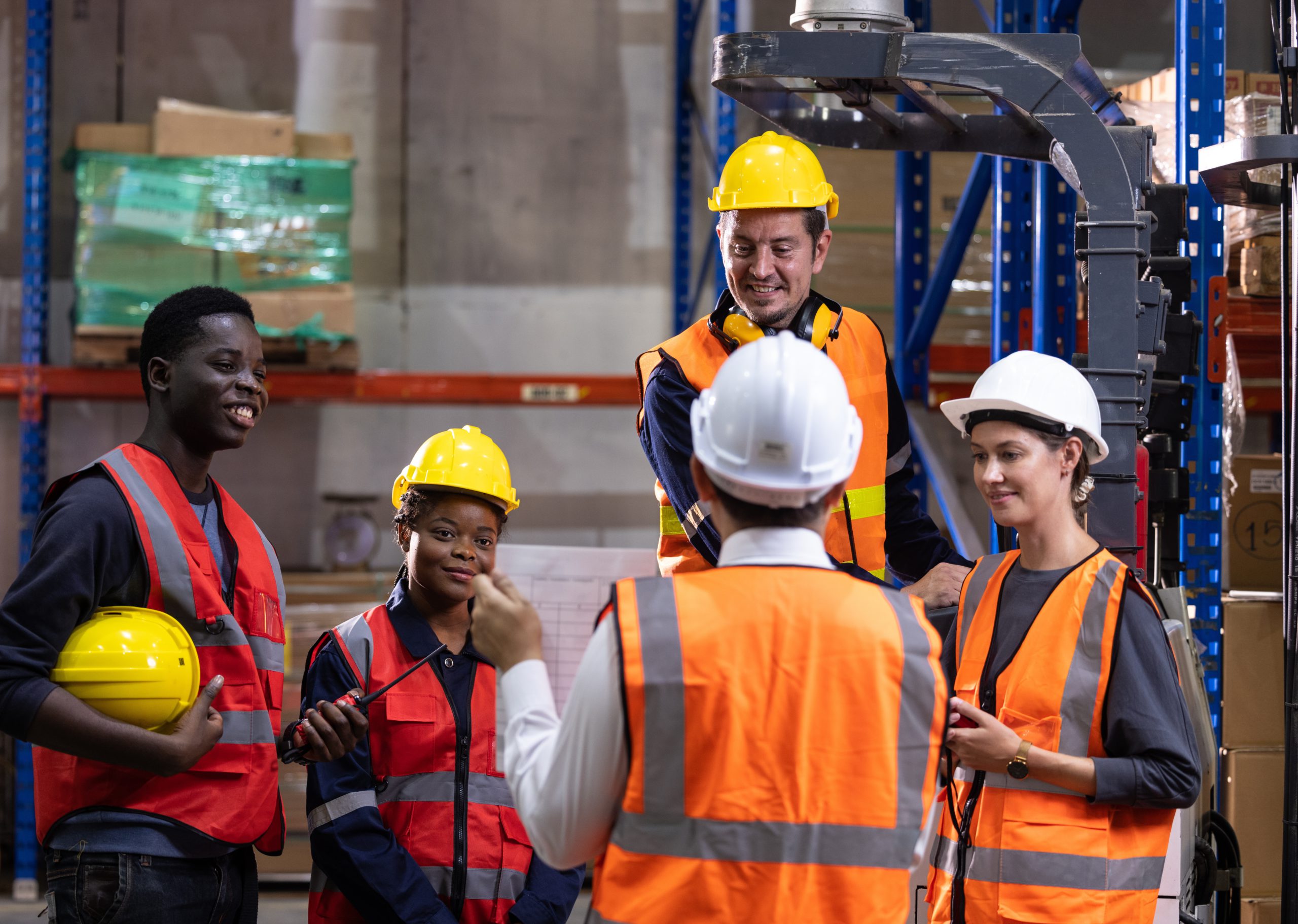
Encouraging a culture of continuous learning is equally important. Empowering workers to embrace technological advancements and adapt to evolving roles through continuous learning initiatives ensures that the workforce remains agile and responsive to industry changes.
Cultivating an agile workforce is key in navigating the dynamic landscape of Industry 4.0. Flexibility and adaptability are vital traits, enabling workers to adjust to new technologies, processes, and market demands swiftly.
“At Partners Personnel we firmly believe that the best way to improve our organization is to foster a culture where our internal staff and the associates we place to work continuously learn and progress,” Partners Personnel President Mark McComb said. “We know that the best return on investment is an investment in our people and this is why we put a premium on training and development.”
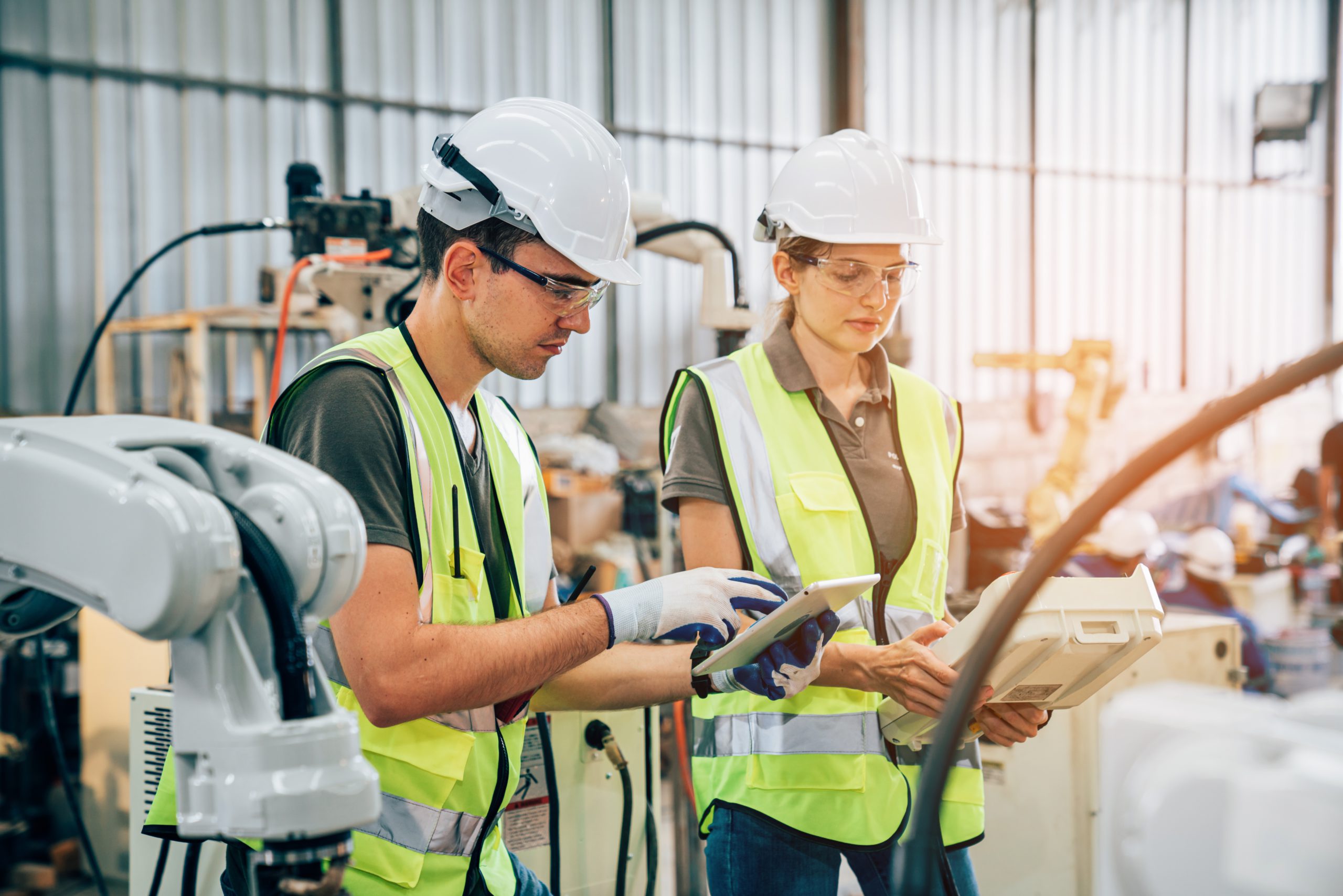
Work With Partners Personnel: A Staffing Agency That Values The Future of Work
In the ever-evolving landscape of Industry 4.0, where the light industrial sector experiences a profound technological shift, finding the right partner becomes crucial for businesses aiming to navigate this transformation successfully. As an expert in light industrial staffing, Partners Personnel stands as an invaluable ally, bridging the gap between cutting-edge technology and a workforce that values safety above all else.
Partners Personnel understands that the impact of Industry 4.0 on the light industrial sector goes beyond technological advancements; it extends to the very core of the workforce. With a profound commitment to employee well-being, Partners Personnel is prepared to meet the challenges and embrace the opportunities presented by automation, AI, and digitization.
Moreover, as a strategic partner, Partners Personnel is dedicated to addressing the challenges associated with Industry 4.0, such as workforce disruption and data security concerns. With a proactive approach to upskilling and fostering a culture of inclusivity, we create an agile and diverse workforce that is well-equipped to embrace the technological advancements of tomorrow.
Embrace the future of work with confidence, knowing that Partners Personnel is committed to safeguarding your workforce’s well-being while maximizing the benefits of Industry 4.0 technologies. Contact your local office today to get started.