In honor of National Safety Month, we got expert advice about workplace safety practices for both clients and associates. On June 1, Partners Personnel invited Ron Swope, it’s National Director of Safety, to present a webinar to its colleagues and stakeholders on best workplace safety practices and how to build a safety-minded workplace culture.
Swope is a veteran of the staffing and safety industries with over 22 years of experience and has held top-secret clearance in a previous role with the U.S. Commerce Department in the Special Police Service. Swope has also received national awards on multiple occasions for his work in creating a world-class risk management and safety program, including Business Insurance Risk Manager of the Year.
In his webinar, “Creating a Safety-minded Culture and Work Environment,” Swope shared two sets of advice. The first concerns how to establish a safe work environment and is encapsulated in the acronym “S.O.R.T.” (Stop, Observe, Recognize, Take Ownership), and the second concerns practices to build a workplace safety culture. Together, these practices and tips will help you organize safety at your workplace from A to Z.
“S.O.R.T.”ing Out Workplace Safety
Swope developed the “S.O.R.T.” system during his own safety training when he attended a presentation and discovered a way to systematically organize workplace facilities from beginning to end that went beyond safety tests or walkthroughs. Thus S.O.R.T. was born to help managers and workers address safety concerns in their proper order.
Employees and supervisors can help each other “S.O.R.T.” their way to a safer work environment with these four steps:
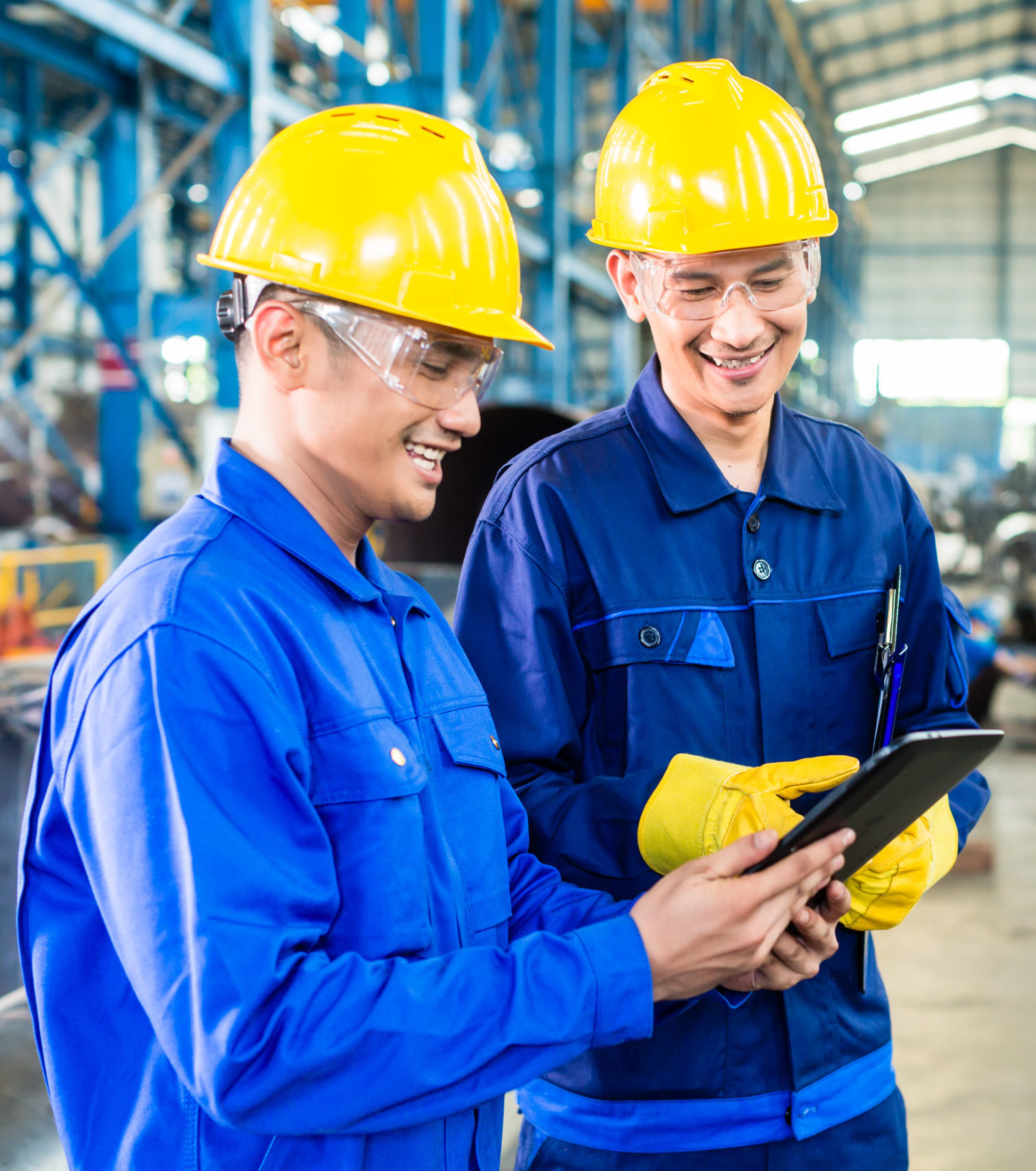
Stop.
Always take time at the beginning of the work shift to evaluate the work area and equipment for any potential hazards. Also be on the lookout for any conditions that could have changed since you were last in the work environment, or since you last used the equipment. Stopping to observe your work area and equipment is important because rushing to do a work task could cause you to miss small but important details. If you notice any changes, stop your work and assess how the situation can be corrected.
Observe.
Next, evaluate the elements of your general environment – the weather conditions, temperature, and lighting. Ask yourself:
- Are all the necessary personnel and tools in place for the task you are about to perform?
- Has your equipment been thoroughly inspected before beginning the task?
- Has all the necessary paperwork been reviewed and completed, such as SOPs, JSAs or permits?
Recognize.
Next, as you’re observing the work area, ask yourself if you see any work hazards. Recognizing hazards comes down to your ability to apply what you’ve learned through training, safety meetings, company policy, lessons learned, safety shares and other past experiences. You need to be able to recognize hazards so you can reduce them and protect yourself and other workplace occupants from injury.
Let’s say you’re loading a machine that has pinch points. Before you load the machine, you need to recognize the potential hazards associated with the whole machine and each of its parts. Taking time to make this recognition before loading it will help you avoid injury to yourself and others in the area when using it.
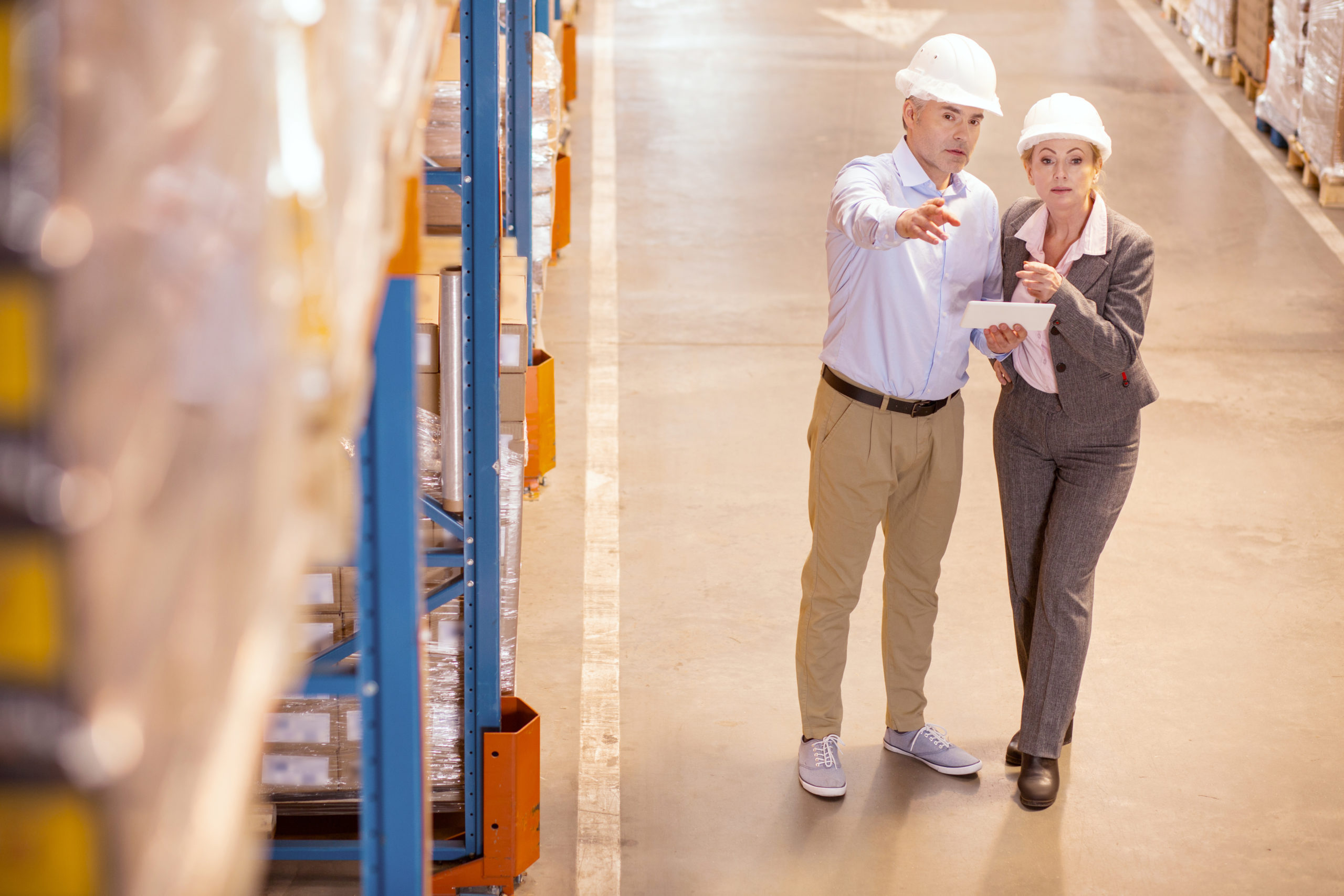
Take Ownership.
Taking ownership is the most important part of S.O.R.T. Own potential hazards once you notice them and work to get them fixed ASAP. Even something as simple as a piece of paper dropped on the floor could present a safety hazard if someone were to step on it, slip and fall. Never walk past a safety hazard – if you see something, say something.
Having the courage to stand up for yourself and others at the workplace is crucial in this step. You are responsible for preventing any hazards that could occur while you’re at the workplace, regardless of what anyone else might think or say. If someone is injured or if property is damaged due to a hazard you recognized but didn’t attend to, that error will continue to affect you long after the incident is past. No one wants to feel guilty about an injury that was due to an unaddressed hazard.
Moreover, what is true for you as an individual employee is also true of the jobsite as a whole. The impacts of a single incident can ripple out from the site of the incident and, depending on its severity, can have far-reaching consequences for the entire company.
For these reasons, it’s important for supervisors and safety managers to encourage everyone at the workplace to take ownership of their responsibility for safety. At the same time, it’s equally important that supervisors and safety managers foster a workplace safety culture in a way that is inviting and not vindictive. No one should be “beaten over the head with the safety stick.” Instead, supervisors and safety managers should extend a hand to their employees and invite them to discuss all safety issues they’ve observed – not only with them but with all workplace occupants.
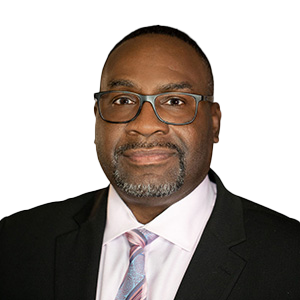
5 Tips To Improve Workplace Safety Culture
Swope believes that, while behavior-based safety is important, workers and supervisors still need to work to build a safety culture at the workplace. But how do you go about doing this? Swope offers 5 tips that he has garnered throughout his career for building or improving the safety culture in the workplace:
1. Look at the big picture.
Safety is a challenge for every company – risks abound, from weather hazards to slips, trips and falls, to machine operating hazards. Therefore, everyone can and should participate in creating a workplace safety culture. In order to do this, you need to take a bird’s-eye view of the safety needs at your specific workplace. Attitude is key to that view – everyone at the workplace needs to recognize that “we’re all in this together.”
From a management perspective, employee buy-in is essential to looking at the big picture of workplace safety. Managers need to raise awareness of their company’s safety program by putting it front and center in their facility.
2. Start at the top.
Management buy-in at all levels is just as important as employee buy-in to creating workplace safety culture. OSHA recommends several practices to enlist management leadership in the design and administration of company safety and health programs. Managers at all levels can contribute to workplace safety culture by:
- Making safety and health core organizational values
- Establishing safety and health goals and objectives
- Setting program expectations and responsibilities
- Providing adequate resources and support for the program
At Partners Personnel, safety culture begins with the CEO and extends through all levels of the company to associates on assignment. Partners associates play a role in workplace safety culture in many ways – through safety tests, safety observations, and various safety trainings – but their participation is made possible in the first place by the CEO’s commitment to workplace safety culture.
Partners also implements workplace safety culture from the top down through GotSafety, a program that provides over 2,000 tailgate lessons, over 800 safety seminars and webinars, OSHA documentation, and customizable digital forms to help promote safety to associates. GotSafety provides a comprehensive program to support workplace safety culture.
3. Put Safety messaging front and center.
Besides helping employees learn their roles and responsibilities, managers need to ensure they know how workplace safety impacts their daily workflow. Managers can provide clear visual and experiential evidence of the company’s commitment to safety by:
- Prominently posting or distributing messaging, such as posters or emails, that clearly communicates the benefits of engaging in workplace safety culture, including incentives for participating in safety initiatives
- Clearly marking pathways that might otherwise present safety hazards
- Providing safety training prior to employees’ first day on the job
- Making sure a safety program is already in place before onboarding employees
- Making sure employees have a voice in that safety program
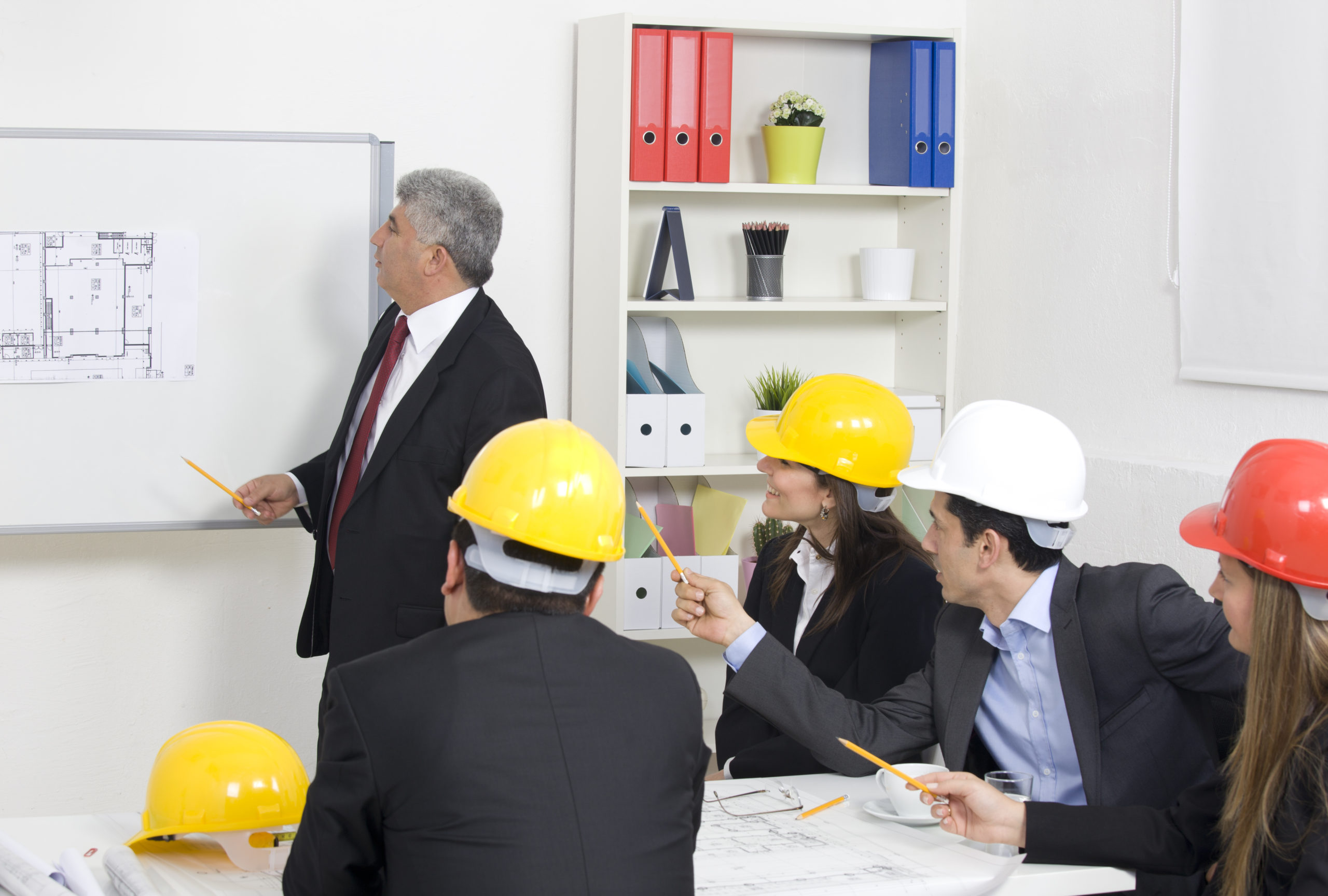
4. Enable two-way communication
Communication is key to developing a workplace safety culture. Employees need to know how to carry out their personal commitment to safety and how to participate in safety and health initiatives. In order to foster communication around workplace safety, supervisors should provide their workers with various ways to make their ideas and concerns known.
One way to do this is by holding regular safety-themed events, like weekly team-based meetings. For example, at the beginning of the workweek supervisors and safety leads can do a walkthrough and then get together with their teams for 15 to 20 minutes for a brief talk about safety issues they’ve discovered as a result of the walkthrough or during the previous week.
No matter what communication method you choose, make it easy for your employees to set personal safety goals, support team safety goals, report accidents or near-misses, and correct behavior without fear of retaliation. In a nutshell: make sure your employees know safety culture is for them and by them.
5. Provide ongoing training.
In addition to providing their workers with open channels of communication about safety, supervisors and safety leads also need to provide ongoing safety training. Regular safety training can:
- Help everyone develop accountability for their safety roles
- Strengthen team relationships
- Give participants an opportunity to learn and practice new skills, such as new machine operation safety guidelines
Supervisors can also arrange educational programs during lunch periods, invite guest speakers and incorporate other interesting activities into the training to add variety to everyone’s daily routine. Conducting these trainings and activities on a regular basis will help everyone keep safety top-of-mind and give them ongoing engagement opportunities to look forward to.
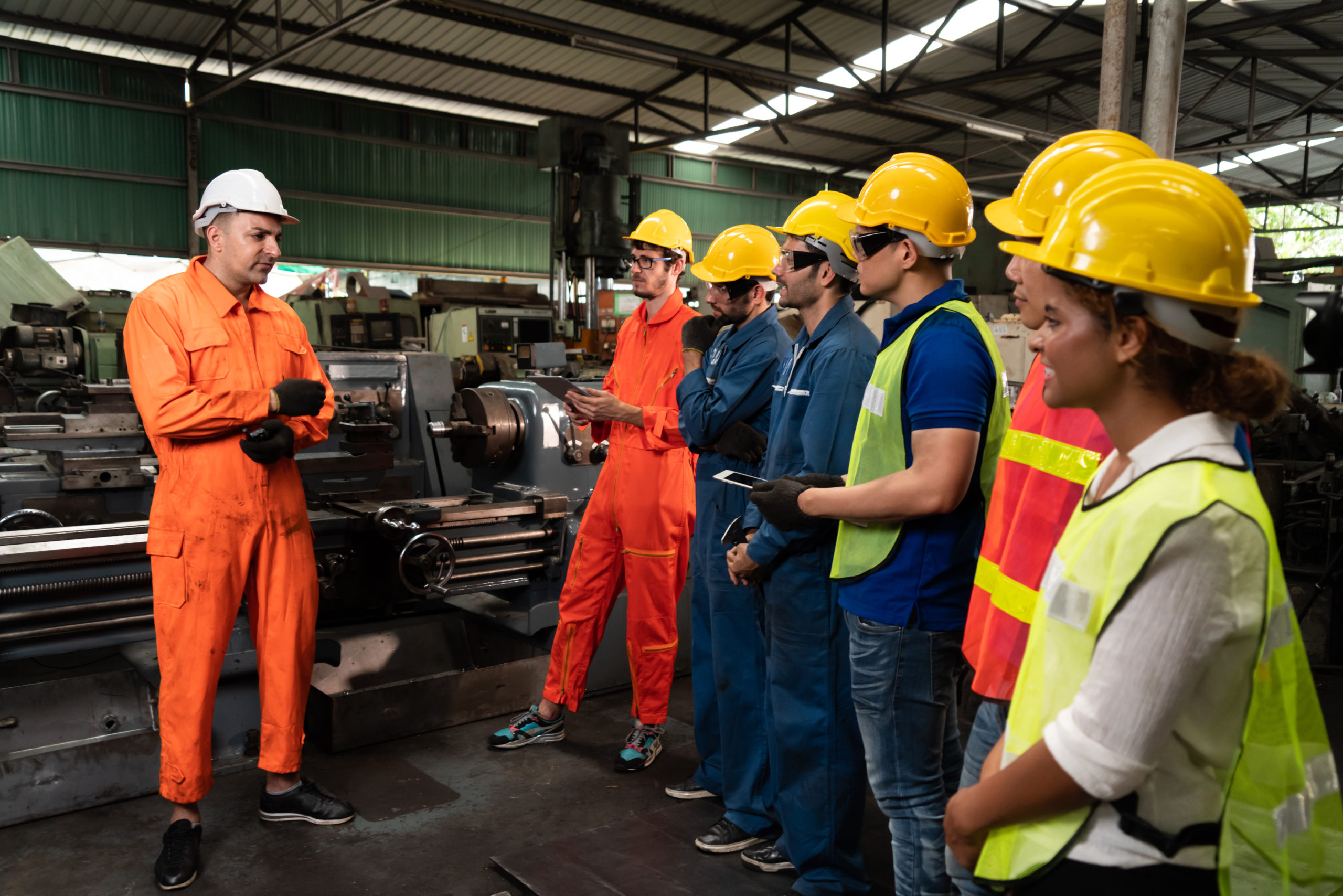
Key Safety Takeaways
Keeping these workplace safety tips in mind can help you prevent unnecessary injury to yourself and others at the workplace. Remembering to “S.O.R.T.” every time you enter the workplace and before beginning a work task will help you and everyone else stay safe on the job. In addition to “S.O.R.T.”ing, you can also help build or improve your workplace’s safety culture by:
- Keeping in mind the big picture of company safety
- Enlisting management at all levels in building workplace safety culture
- Putting safety messaging front and center
- Maintaining open two-way communication around safety
- Providing ongoing safety training and other safety activities
If you ever have any questions about workplace safety, or ideas for improving it, please don’t hesitate to share them with a Partners Personnel supervisor or safety manager. We want you to know that your feedback is valued, because Partners Personnel values everyone’s safety at work. Let’s help each other build a solid workplace safety culture!
Want more safety best practices? Have a look at “4 Summer Workplace Safety Tips for National Safety Month,” “30 of the Best Branch Safety Practices” and advice on how to avoid slips, trips and falls at work.
Partners specialists love helping people find safe, great-fitting jobs. If you’re looking for your next employment opportunity, we can help! Visit our website and begin your search today: www.partnerspersonnel.com/